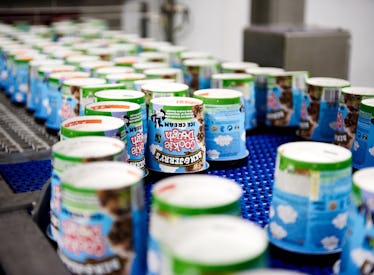
Ben & Jerry’s, a producer of various unique flavours of ice cream and part of Unilever, had an ambitious goal. The company wants to build a smart factory in which virtually all production processes are fully automated. One of the steps involved in the realisation of this smart factory concerns the implementation of a new digital information system.
The old production site consisted of a number of individual production lines with no connections between them. The operator received orders via forms and had to process a wealth of information by hand. With this system, Ben & Jerry's wanted to make improvements in four key areas. It had to connect the various production lines to one another, the software had to take over various administrative tasks, the occurrence of errors on the product packaging had to be minimised and work had to be taken out of the operators’ hands to allow them to focus more on the production process itself. Ben & Jerry’s chose Visual Link Software's Manufacturing Execution System (VLS|MES) to realise these goals.
The first step was to digitise the production lines. This was done by installing additional sensors, establishing links to machine controls and measuring equipment and storing all these data in a central database. In total, 15,000 measuring points (sensors) were installed in more than 100 machines. This results in a vast quantity of data, which can be divided into two main streams. Data stream 1 concerns data sent from the office environment to the production floor. Think of e.g. production information derived from orders or data for the lot code printer that automatically prints the correct use-by date on the bottom of the tubs. Data stream 2 concerns data that the system retrieves from the production floor. This includes produced quantities, average weights from the weighing points, the number of rejected products, machine activity and order status.
This process of digitisation and the centralised storage of all data in a single powerful database ensures that the planning of production runs takes far less time and lines can be used more efficiently. This gives operators far more time to better manage the process and produce optimal products.
Using software to take over administrative tasks, e.g. to ease the workload of operators
In the past, operators would receive production orders on forms. They then had to enter all relevant information into the production system by hand, which was both time consuming and prone to errors. As the demand for diversity grew, product quality requirements increased and more different types of production runs had to be completed, it became impractical to keep doing all this by hand. Operators were spending more and more time entering all the information. By digitising this process, the relevant order information is sent directly from the office environment to the production system. This has all but eliminated the operator's administrative workload, so they can focus their attention on the production process itself.
Minimising errors on the product packaging
With more than forty different flavours of ice cream that are exported to countries all over the world, it is important that the right product ends up in the right packaging and that text is printed in the right language. Besides the fact that consumers expect to see text in their own language on a product's packaging, this is also required by law. Ben & Jerry's wanted to be sure that the contents, the packaging and the order that was entered all matched up. Together with a prominent supplier of Vision equipment, VLS|MES developed a solution for this issue. During the production process, the Vision camera reads the production code on each packaging. These data are recorded in the VLS|MES database and the system then checks if the code is correct. If it is not, the product with the incorrect code is removed from the production line and an analysis is conducted to find out at what stage of the process something went wrong, so the necessary measures can be taken.
Result
The Ben & Jerry's facility in Hellendoorn is now one of the multinational’s most highly automated ice cream factories. All production processes and steps for the entire factory were made insightful using a single reliable and user-friendly digital system. VLS|MES will allow Ben & Jerry's to gradually uncover the major issues and further optimise its production process one step at a time.
Ben & Jerry's is an American ice cream producer that is based in Vermont in the United States. The company was founded in 1978 and its products have been available in the Netherlands since 1996. The company was sold to Unilver in 2000. The ice cream for the European market is produced at a Unilever site in Hellendoorn.